Толчок к устойчивости изменил отрасли промышленности, и автомобильное производство не является исключением. Фабрики по всему миру переосмысливают процессы для снижения воздействия на окружающую среду при сохранении высококачественного производства. Сейчас, Современный фабричный фабричный кабинет стеклоочистителя находится в авангарде этих изменений, Интеграция экологически чистых практик для революции его производства. Этот блог выявит, как он отвечает растущему спросу на более зеленые автомобильные решения, прокладывая путь для более ответственной отрасли.
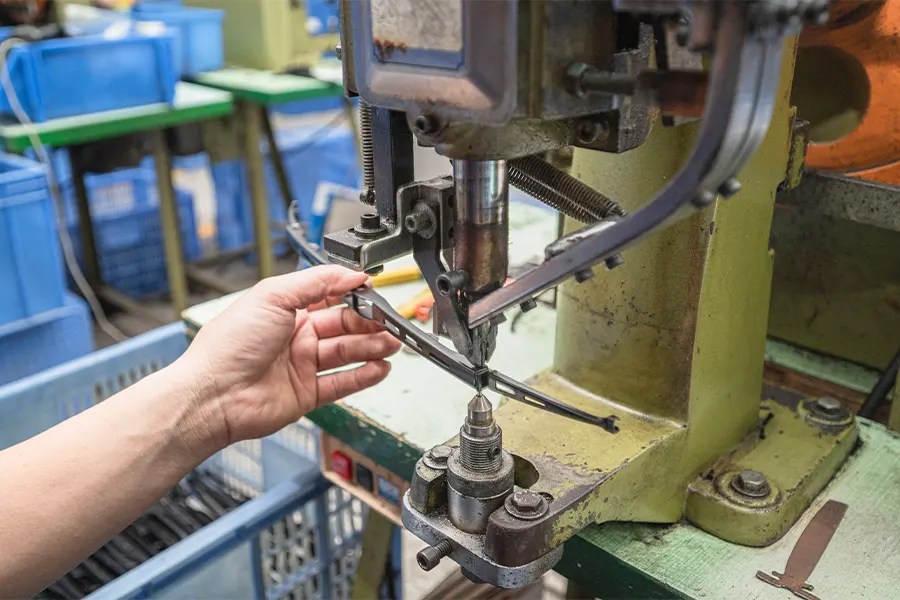
Выберите устойчивые материалы
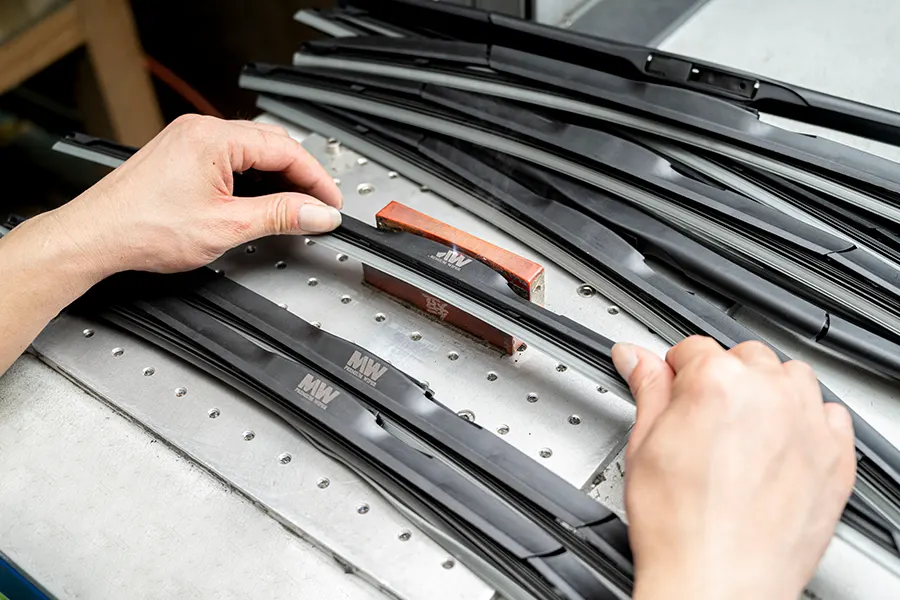
Устойчивость начинается с вдумчивого выбора материала. Производители лезвия стеклоочистителей, такие как Clwiper, переходят к экологически чистым альтернативам, чтобы минимизировать экологическое воздействие. Здесь используются общие устойчивые материалы:
- Натуральный каучук: Получен из резиновых деревьев, Этот возобновляемый ресурс предлагает превосходную эластичность и долговечность, Сделать его более зеленой альтернативой синтетическому резине.
- Биоссовые полимеры: Они производятся из возобновляемых источников, таких как кукурузный крахмал или сахарный тростник, Предлагая устойчивый вариант для компонентов лезвия.
- Переработанные металлы: Металл с отломки для структурных элементов уменьшает необходимость добывать новые ресурсы, снижение воздействия на окружающую среду.
- Силиконовая резина: Хотя не биоразлагаем, Силикон высокого класса длится долгое время и уменьшает отходы из-за расширенного жизненного цикла.
- Растительное подкрепление: Усиление волокна, полученные из таких растений, как джут или конопля.
Повысить энергоэффективность
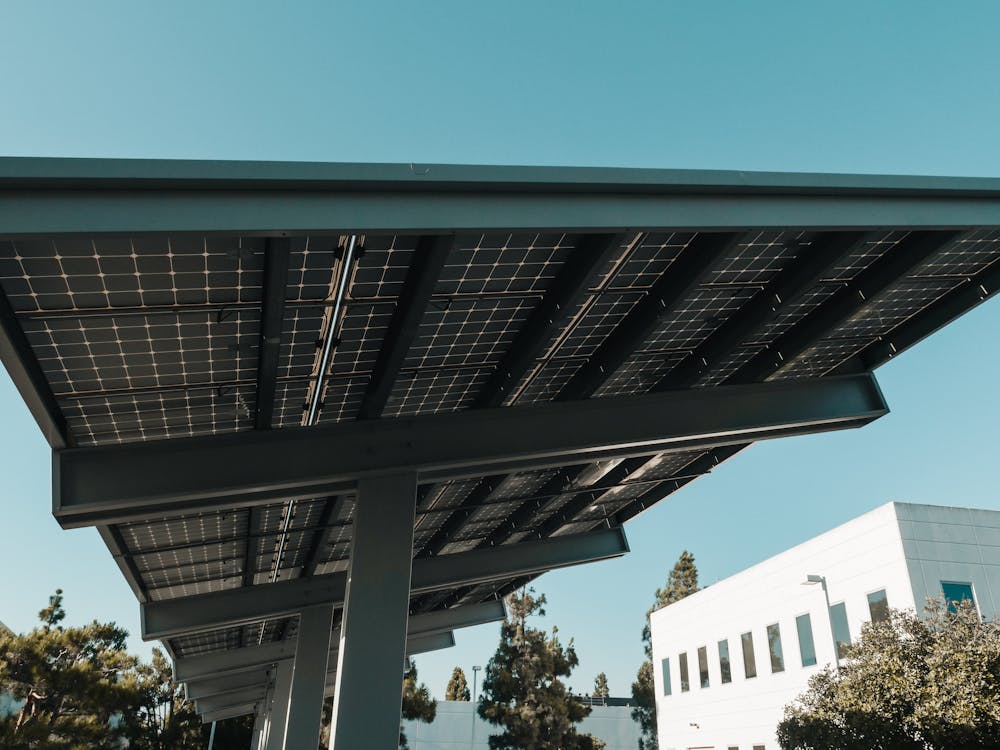
Повышение энергоэффективности является краеугольным камнем устойчивого Производство В индустрии лезвий стеклоочистителей. Многие фабрики переходят к возобновляемым источникам энергии, с солнечными панелями, установленными на крышах, генерируя до 30% о потребностях в энергетике объекта. Этот сдвиг уменьшает зависимость от ископаемого топлива и значительно снижает выбросы углерода.
Для дальнейшего повышения эффективности, Усовершенствованные экструзионные машины заменяют более старые модели. Эти современные системы потребляют 20% меньше электричества, оптимизация производства без ущерба для качества. Наряду с этими машинами, Суммары с интеллектуальными производственными системами, управляемыми ИИ, революционизируют операции. Мониторинг производственных линий в режиме реального времени, Эти системы оптимизируют использование механизма, уменьшить время холостого хода, и сократить энергетические отходы до 15%.
Инициативы по возобновляемой энергии также распространяются на ветряные турбины, которая дополняет генерацию солнечной энергии. Фабрики, интегрирующие эти технологии, сообщают о существенном сокращении выбросов CO2, эквивалентно выводу тысяч автомобилей с дороги каждый год. Вместе, Эти достижения демонстрируют, как инициативы по энергоэффективности могут беспрепятственно смешиваться с производственными процессами, при этом принося пользу как окружающей среде, так и в эксплуатационных затратах.
Следуйте стратегиям сокращения отходов
Сокращение отходов стало жизненно важным направлением для каждого прогрессивного поставщика лезвия стеклоочистителей. Фабрики внедряют методы производства бережливого производства, чтобы минимизировать избыточное использование материала, Обеспечение того, чтобы каждый необработанный ресурс способствовал конечному продукту. Этот подход не только уменьшает отходы, но и оптимизирует эффективность производства.
Утилизация также играет важную роль в этих стратегиях. Резумия на лом из производственных линий перепроизводится в вторичные продукты, такие как промышленные полы или изоляционные материалы, Предотвращение его въезда в свалки. Сходным образом, Металлические отделки растоплены и повторно используются в производственных процессах, Создание системы с замкнутым контуром, которая максимизирует эффективность ресурсов.
Системы управления цифровыми запасами также помогают поставщикам отслеживать использование материалов с точностью. Анализируя данные в режиме реального времени, Фабрики могут предвидеть нехватку или избыток, сокращение перепроизводства и ненужных отходов.
Следуйте методам сохранения воды
Сохранение воды является ключевым элементом для уменьшения воздействия производства лезвий стеклоочистителя на окружающую среду. Многие фабрики, такие как Clwiper, какая переработка воды, используемой в производственных процессах, Минимизация потребности в пресной воде. Этот подход гарантирует, что вода повторно используется эффективно, лечится от чистоты, и вернулся в производственный цикл, сокращение отходов и истощения ресурсов.
В дополнение к этим системам, фабрики включают методы сбора дождевой воды. Захватив дождевую воду, Производители снижают свою зависимость от муниципальных источников воды, направлять его на несущественное использование, например, системы охлаждения и очистка объектов. Эта устойчивая практика помогает сохранить ценную питьевую воду для других целей.
Для дальнейшего минимизации потребления воды, Современный механизм был разработан, чтобы использовать меньше воды, сохраняя при этом высокий уровень производительности. До 30% требуется меньше воды по сравнению с традиционным оборудованием, сделать весь процесс более эффективным и экологически ответственным.
Приняв эти стратегии экономии воды, Фабрики не только снижают эксплуатационные расходы, но и способствуют глобальным усилиям по сохранению водных ресурсов.
Повышение инноваций в упаковке
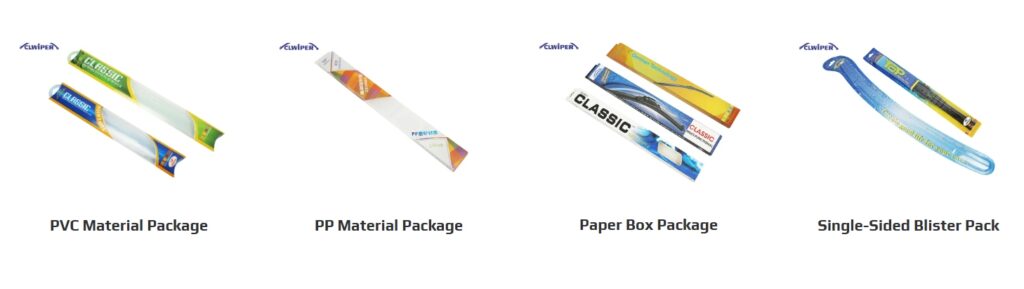
Инновационная упаковка является важным элементом в устойчивой практике современного производства. КЛИППЕР, анонца OEM Wiper Blade продюсер, Ведущий путь, используя экологически чистые варианты упаковки, которые минимизируют отходы и снижают воздействие на окружающую среду. Он уходит от традиционной пластиковой упаковки, выбирая более устойчивые альтернативы, такие как Без ПВХ и стр (полипропилен) материалы. Эти материалы не только обеспечивают долговечность и прочность, но также полностью пригодны для переработки, обеспечение более длительного жизненного цикла и сокращение потребности в новом сырье.
Кроме того, бумажная упаковка набирает обороты. Для замены пластиковых контейнеров используются опции для переработки картон и картон и картона., Предложение биоразлагаемой и компостируемой альтернативы, которая соответствует целям глобальной устойчивости. Сдвиг на бумагу также позволяет производителям снизить вес упаковки, Оптимизация эффективности доставки и снижение выбросов углерода от транспорта.
Для более деликатных компонентов лезвия стеклоочистителей, это принят Односторонние блистерные пакеты. Эти пакеты, сделано из переработанных материалов, Предложите легкое, но защитное упаковочное решение. Они не только снижают потребность в чрезмерном пластике, но и повышают видимость продукта для потребителей, Предоставление привлекательного и экологически чистого дисплея.
Этот сдвиг соответствует потребительскому спросу на более экологичные продукты и поддерживает экологическое управление на протяжении всего производства.
Заключение
Экологически чистые производственные практики изменяют индустрия лезвий стеклоочистителя.. Фабрика лезвия стеклоочистителя, такая как Clwiper, которая приоритетов устойчивости ведет к тому, что вы найдете зеленые материалы, сокращение отходов, сохранение воды, и использовать энергоэффективные технологии. Инновации в упаковке дополнительно подчеркивают их приверженность защите окружающей среды. Эти усилия гарантируют, что фабрики могут соответствовать ожиданиям потребителей при защите планеты, Установка стандарта для очистки, зеленое будущее в автомобильном производстве.